Французький інститут сонячної енергетики INES розробив нові фотоелектричні модулі з термопластами та натуральними волокнами з Європи, такими як льон і базальт.Вчені прагнуть зменшити вплив сонячних панелей на навколишнє середовище та зменшити вагу, а також покращити переробку.
Панель із переробленого скла спереду та льняного композиту ззаду
Зображення: GD
З журналу pv France
Дослідники Французького національного інституту сонячної енергії (INES) – підрозділу Французької Комісії з альтернативних джерел енергії та атомної енергії (CEA) – розробляють сонячні модулі з новими біоматеріалами на передній і задній сторонах.
«Оскільки вуглецевий слід і аналіз життєвого циклу стали основними критеріями вибору фотоелектричних панелей, пошук матеріалів стане вирішальним елементом у Європі в найближчі кілька років», — сказав Аніс Фуіні, директор CEA-INES. , в інтерв’ю журналу pv France.
Од Дерріє, координатор дослідницького проекту, сказала, що її колеги розглянули різні матеріали, які вже існують, щоб знайти той, який міг би дозволити виробникам модулів виробляти панелі, які покращують продуктивність, довговічність і вартість, одночасно знижуючи вплив на навколишнє середовище.Перший демонстратор складається з сонячних елементів з гетеропереходом (HTJ), інтегрованих у повністю композитний матеріал.
«Лицька сторона зроблена з полімеру, наповненого скловолокном, який забезпечує прозорість», — сказав Дерріє.«Тильна сторона зроблена з композиту на основі термопластику, в який інтегровано переплетення двох волокон, льону та базальту, що забезпечить механічну міцність, а також кращу стійкість до вологи».
Льон вивозять із північної Франції, де вже присутня вся промислова екосистема.Базальт добувається в інших країнах Європи та плететься промисловим партнером INES.Це зменшило вуглецевий слід на 75 грам CO2 на ват порівняно з еталонним модулем такої ж потужності.Вага також була оптимізована і становить менше 5 кілограмів на квадратний метр.
«Цей модуль призначений для інтеграції фотоелектричної системи на даху та будівлі», — сказав Дерріє.«Перевагою є те, що він має природний чорний колір, без підкладки.З точки зору переробки, завдяки термопластам, які можна переплавити, поділ шарів також є технічно простішим».
Модуль можна зробити без адаптації поточних процесів.Дерріє сказав, що ідея полягає в тому, щоб передати технологію виробникам без додаткових інвестицій.
«Єдина обов’язкова умова полягає в тому, щоб мати морозильні камери для зберігання матеріалу, а не для запуску процесу зшивання смоли, але більшість виробників сьогодні використовують препрег і вже мають для цього обладнання», — сказала вона.
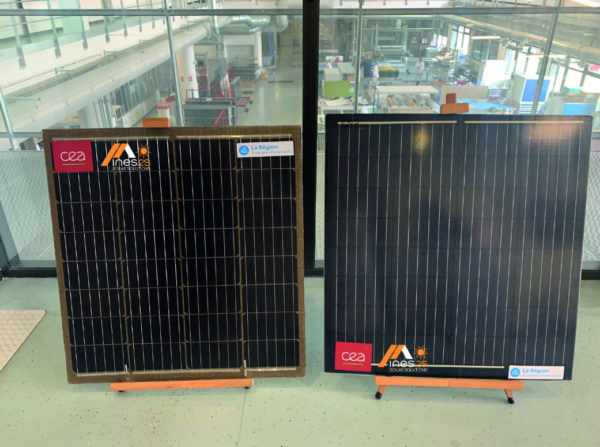
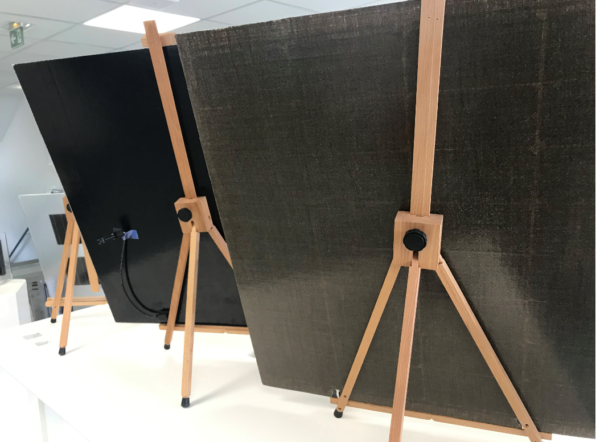
«Ми працювали над другим життям скла та розробили модуль, виготовлений із повторно використаного скла товщиною 2,8 мм зі старого модуля», — сказав Дерріє.«Ми також використали термопластичний герметик, який не вимагає зшивання, тому його буде легко переробити, а також термопластичний композит із волокном льону для стійкості».
Безбазальтова тильна сторона модуля має натуральний колір льону, що може бути естетично цікавим для архітекторів, наприклад, з точки зору інтеграції у фасад.Крім того, інструмент розрахунку INES показав зменшення вуглецевого сліду на 10%.
«Тепер вкрай необхідно поставити під сумнів ланцюги постачання фотоелектричної енергії», — сказав Джуїні.«Тому за допомогою регіону Рона-Альпи в рамках Міжнародного плану розвитку ми шукали гравців за межами сонячного сектору, щоб знайти нові термопластики та нові волокна.Ми також думали про поточний процес ламінування, який дуже енергоємний».
Між фазою підвищення тиску, пресування та охолодження ламінування зазвичай триває від 30 до 35 хвилин з робочою температурою приблизно від 150 C до 160 C.
«Але для модулів, які все більше включають екологічно розроблені матеріали, необхідно перетворювати термопластики при температурі приблизно від 200 C до 250 C, знаючи, що технологія HTJ чутлива до тепла і не повинна перевищувати 200 C», — сказав Дерріє.
Науково-дослідний інститут об’єднується з французькою компанією Roctool, яка спеціалізується на індукційному термостиску, щоб скоротити тривалість циклу та виготовляти форми відповідно до потреб клієнтів.Разом вони розробили модуль із задньою стороною, виготовленою з поліпропіленового термопластичного композиту, до якого вбудовано перероблене вуглецеве волокно.Лицьова сторона виконана з термопластику і скловолокна.
«Процес індукційного термостиску Roctool дає змогу швидко нагріти дві передню та задню пластини, не досягаючи 200 C у серцевині клітин HTJ», — сказав Дерріє.
Компанія стверджує, що інвестиції нижчі, і процес може досягти часу циклу всього в кілька хвилин, використовуючи при цьому менше енергії.Технологія спрямована на виробників композитних матеріалів, щоб дати їм можливість виготовляти деталі різних форм і розмірів, використовуючи легші та міцніші матеріали.
Час публікації: 24 червня 2022 р