Французький інститут сонячної енергії INES розробив нові модулі PV з термопластиками та природними волокнами, що виникають у Європі, такі як льон та базальт. Вчені прагнуть зменшити екологічний слід та вагу сонячних батарей, одночасно покращуючи переробку.
Перероблена скляна панель спереду та білизна композиція на задній частині
Зображення: GD
З журналу PV France
Дослідники Національного інституту сонячної енергії Франції (INES)-відділення Французької альтернативної енергії та комісії з атомної енергії (CEA)-розробляють сонячні модулі, що містять нові матеріали на основі біо-на основі передньої та задньої сторони.
"Оскільки вуглецевий слід та аналіз життєвого циклу тепер стали важливими критеріями у виборі фотоелектричних панелей, пошук матеріалів стане вирішальним елементом у Європі в найближчі кілька років",-сказав Аніс Фуїні, директор Cea-ines , в інтерв'ю журналу PV France.
Оуд Дер'єр, координатор дослідницького проекту, заявив, що її колеги розглядали різні матеріали, які вже існують, щоб знайти той, який міг би дозволити виробникам модулів виробляти панелі, що покращують продуктивність, довговічність та вартість, знижуючи вплив на навколишнє середовище. Перший демонстратор складається з гетероперехідних (HTJ) сонячних батарей, інтегрованих у всекомпозитний матеріал.
"Передня сторона виготовлена з наповненого склопластиком полімеру, що забезпечує прозорість",-сказав Дер'єр. "Задня сторона виготовлена з композиту на основі термопластиків, в яких було інтегровано плетіння двох волокон, льону та базальту, що забезпечить механічну міцність, але також кращу стійкість до вологості".
Льон отримує з Північної Франції, де вже присутня вся промислова екосистема. Базальт виходить в інших місцях Європи і витканий промисловим партнером INES. Це зменшило вуглецевий слід на 75 грам CO2 на ват, порівняно з еталонним модулем тієї ж потужності. Вага також була оптимізована і становить менше 5 кілограмів на квадратний метр.
"Цей модуль спрямований на PV на даху та інтеграцію будівництва", - сказав Дер'єр. «Перевага полягає в тому, що він природно чорний колір, без потреби в зворотній таблиці. З точки зору переробки, завдяки термопластичній, яку можна переробити, розділення шарів також технічно простіше ».
Модуль може бути зроблений без адаптації поточних процесів. Дер'єр сказав, що ідея полягає у передачі технології виробникам, без додаткових інвестицій.
"Єдиний імператив-мати морозильні камери для зберігання матеріалу, а не розпочати процес зшивання смоли, але більшість виробників сьогодні використовують препрег і вже для цього готові",-сказала вона.
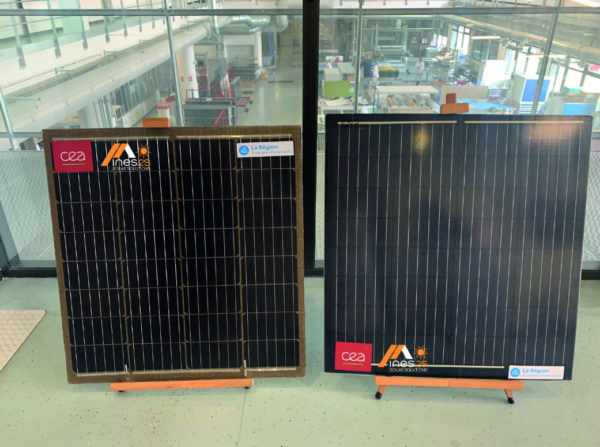
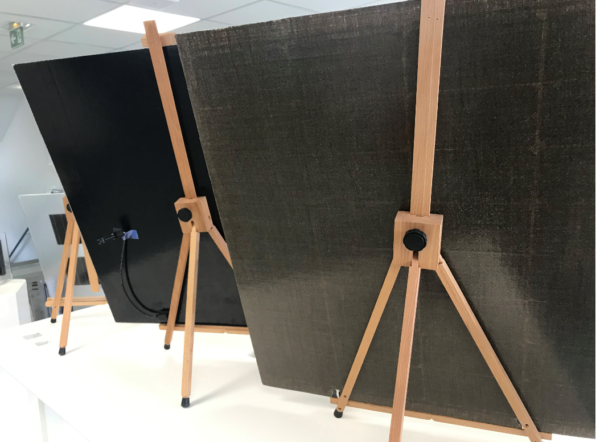
"Ми працювали над другим життям скла і розробили модуль, що складається з повторного використання 2,8 мм скла, що виходить зі старого модуля", - сказав Дер'єр. "Ми також використовували термопластичний інкапсулант, який не потребує зшивання, що, отже, буде легко переробити, і термопластичний композит з льоновим волокном для стійкості".
Задня частина модуля без базальту має природний колір білизни, що може бути естетично цікавим для архітекторів з точки зору інтеграції фасаду. Крім того, інструмент обчислення INES показав 10% зниження вуглецевого сліду.
"Зараз важливо ставити під сумнів фотоелектричні ланцюги поставок", - сказав Джойні. «За допомогою регіону Рона-Альп в рамках міжнародного плану розвитку ми пішли шукати гравців поза сонячним сектором, щоб знайти нові термопластики та нові волокна. Ми також подумали про поточний процес ламінування, який є дуже інтенсивним енергією ».
Між тиском, натисканням та фазою охолодження, ламінування зазвичай триває від 30 до 35 хвилин, з робочою температурою від 150 до 160 с.
"Але для модулів, які все частіше включають екологічні матеріали, необхідно перетворити термопластики приблизно при 200 С до 250 С, знаючи, що технологія HTJ чутлива до тепла і не повинна перевищувати 200 С",-сказав Дер'єр.
Дослідницький інститут об'єднується з Францією, що базується на франції, спеціалістом з термокомпресії Roctool, щоб скоротити час циклу та зробити форми відповідно до потреб клієнтів. Разом вони розробили модуль із задньою обличчям, виготовленим з термопластичного композиту поліпропіленового типу, до якого інтегровані перероблені вуглецеві волокна. Передня сторона виготовлена з термопластики та склопластику.
"Процес індукційної термокомпресії Roctool дозволяє швидко нагріти два передні та задні пластинки, не добираючись до 200 С в основі клітин HTJ", - сказав Дер'єр.
Компанія стверджує, що інвестиції нижчі, і процес може досягти часу циклу всього декількох хвилин, використовуючи менше енергії. Ця технологія спрямована на композитних виробників, щоб дати їм можливість виробляти частини різних форм і розмірів, одночасно інтегруючи легші та більш міцні матеріали.
Час посади: 24-2022 червня